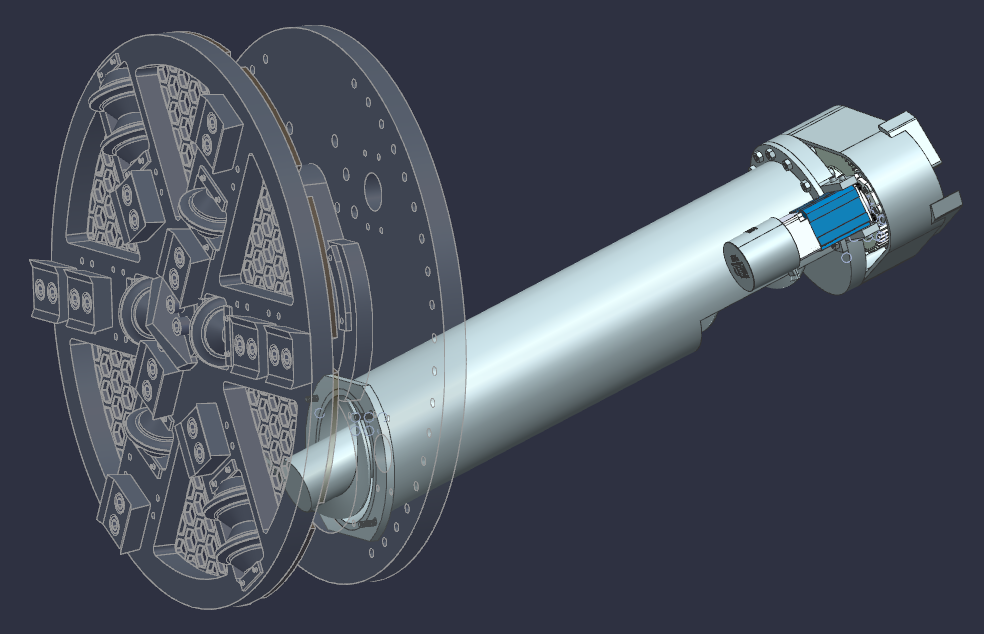
Custom Screw Conveyor
Sub-assembly tasked with material transfer from the front to the rear of the tunnel boring machine by handling large chunks of sedimentary rock.
Learn moreEntirely Undergrad Engineering Team, Here to make Kick ass engineers
UMD Loop is a competition team part of the University of Maryland. All our members are undergraduate students, and we take pride in balancing our studies with the work on this engineering team. We competed in the Not-a-Boring Competition, where we were tasked with digging a 100 feet long tunnel that is 2 feet in diameter. In the first-ever competition, we won the safety award for our outstanding systems analysis and verification to ensure safety of the team and the public. Currently, we are looking to make a debut in the University Rover Challenge where we build a martian rover capable of navigating NASA's Mars Desert Research Station in the deserts of Utah.
I started as the responsible engineer for a material transfer assembly called the screw conveyor. With that role, I designed, analyzed, and assembled this conveyor. The parts I designed came to fruition with detailed drawings and deliberation with machinists. As time progressed and members started graduating, I was involved in other sub-assemblies, namely the transmission and excavation tools. These last two items were in dire needs of development as the competition was drawing near. During major crunch time, my team and I completed and assembled the excavation sub-assembly while learning valuable experience in tolerances and hands-on assembling. The screw conveyor was an engineering trial from the beginning. Having no prior knowledge in material transfer systems and conveyors, I sought out governing equations for screw conveyors to optimize the screw conveyor sizing for our needs.
Sub-assembly tasked with material transfer from the front to the rear of the tunnel boring machine by handling large chunks of sedimentary rock.
Learn moreDetermined tolerances and the appropriate processes to create and assemble the tools and transmission of the excavation sub-assembly.
Learn moreGoing into the second Not-a-Boring Competition, I was the lead engineer for the excavation subteam. I wanted to share my experience and skillset learned from the first competition to new members while also expanding upon them in the second competition. It was a learning experience to transition from purely technical work to technical and systems level work. While still actively designing and analyzing, I had to put equal effort into planning requirements and logistics for the team to succeed, not just myself.
I guided the subteam with setting relevant requirements based on our system's development. Delegating members to different tasks required the facilitation of knowledge transfers from either myself or other core members of the team. I particularly transferred knowledge on modeling in NX 11, using finite element analysis on our new components, and knowing what loads acted on our components. While I opted for a hands off approach in distributing tasks, I still wanted to be involved in major design breakthroughs and back up our member's decisions
The team wanted to transition to a new competition called the University Rover Challenge after the Not-a-Boring Competition. Going into this newer competition, I strove to build upon my past experience as Excavation Lead and improved my communication among my members. There was also better motivation to compete in something new.
This competition, we are focusing on simulating the motion and dynamics of our models first before investing time to building physical prototypes. Without sinking costs into creating physical prototypes of every potential suspension design, I investigated the usage of multi-body dynamics (MBD) software and taught other members how to use it for our complex mechanisms. We vetted the software against existing literature that used 2D quasistatic force analysis.